Improve the efficiency of pharmaceutical distribution and disaster response in the Tokyo metropolitan area
Large and Highly-Functional Logistics Center
TBC DynaBASE
TBC DynaBASE is a logistics center with cutting-edge technologies for prescription pharmaceuticals built in the “Keihin Truck Terminal,” an area designated by the Tokyo Metropolitan Government as a wide-area transportation base in the event of a disaster. TBC DynaBASE was the first in Japan to be licensed by the Tokyo Metropolitan Government as a joint distribution and delivery center for pharmaceutical wholesalers to share storage space for pharmaceutical products, by completely managing the storage location of pharmaceuticals by computer based on a highly functional system. In addition, we are taking on the challenge of innovation in pharmaceutical distribution, including thorough automation through the active introduction of state-of-the-art robots and dramatic improvements in logistics efficiency.
Pharmaceutical distribution – TBC DynaBASE is the ultimate in disaster preparedness and automation.
It is located very close to the Tokyo Metropolitan Government’s disaster prevention facilities, disaster base hospitals, and Haneda Airport, and is located at the Tokyo Metropolitan Government’s designated wide-area transportation base for disasters. It is the only distribution center for prescription pharmaceuticals within Ring Road No. 7, and also serves as a base for the distribution of pharmaceuticals in the event of a disaster, such as an earthquake directly under the Tokyo metropolitan area. TBC DynaBASE and TBC WILL Shinagawa, which is also located within Ring Road No.7, divide their responsibilities to ensure full disaster preparedness in the Tokyo metropolitan area.
Disaster response in the Tokyo metropolitan area
Being located inside the Loop Road No. 7 and near “Ariake-no-Oka,” the main wide-area disaster management base facility, it’s capable of providing pharmaceuticals promptly and smoothly in the event of a disaster such as the Tokyo Inland Earthquake. A seismic isolation structure is used not only for the buildings but also for the adjacent rampway (slope passage). In addition, equipped with a large private power generator (5,000 kVA), it can run at full capacity for 72 hours during emergencies.
Also, with uninterruptible power source equipment installed in the distribution server, facility controller, communication facilities, etc., it can deal with instantaneous blackouts that may occur when switching to the private power generator.
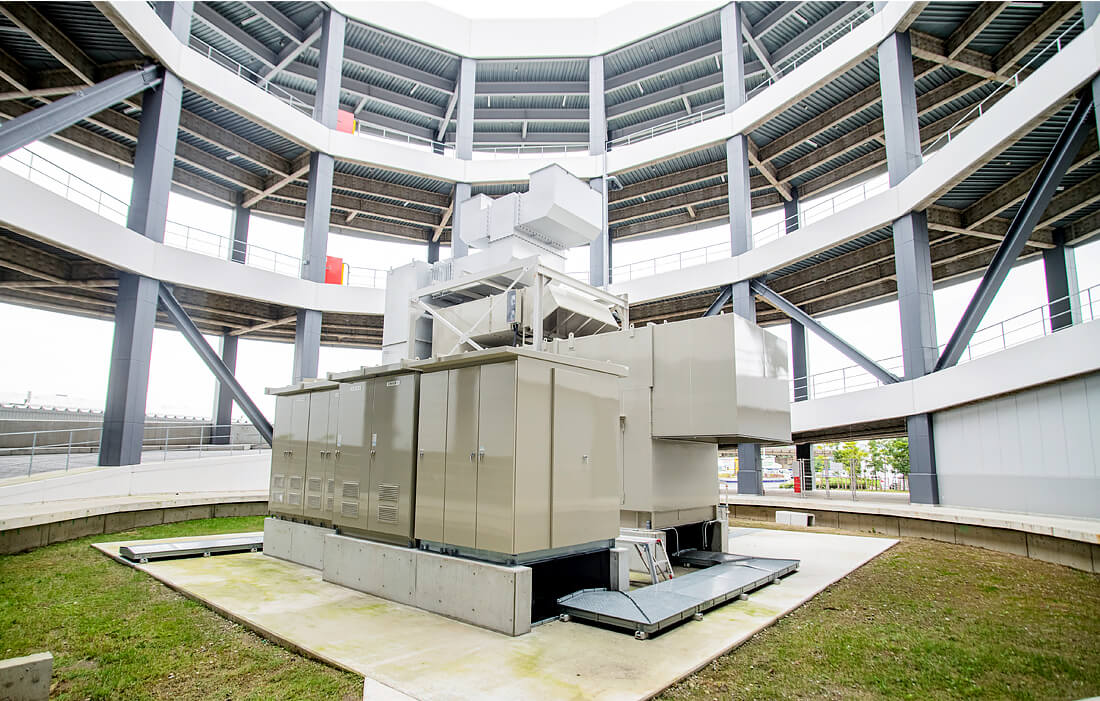
The world’s highest-level automation technologies
In preparation for a shrinking workforce due to the declining birthrate and aging population, as well as for large-scale disasters, we have long been working to automate our distribution centers. Robots for picking products were introduced at TBC Saitama, which began operations in 2014. Since then we have continued to push forward with the introduction of automation technology, achieving a 95% automation rate for picking at TBC DynaBASE. Furthermore, we have achieved shipping accuracy exceeding the 99.99999% recorded by conventional distribution centers. In addition to automated warehouses and picking robots, we have introduced cutting-edge equipment such as conveyors equipped with a highly functional sorter (automatic sorter) to further increase operational efficiency.
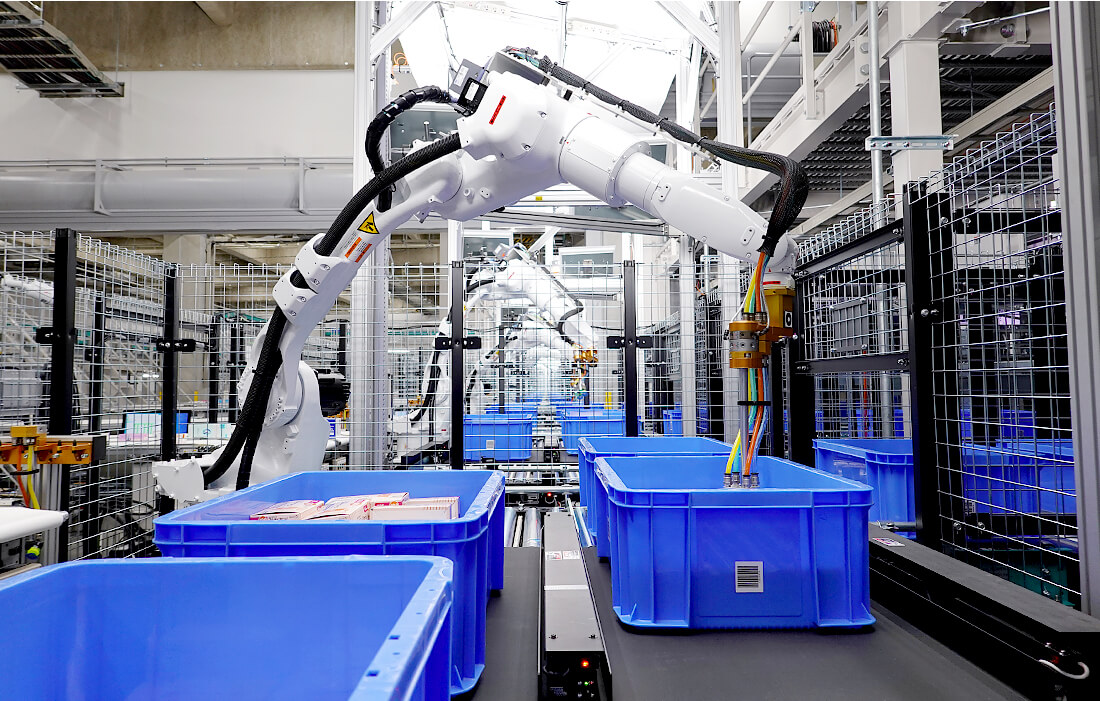
Realization of joint distribution
Since thorough traceability is essential for pharmaceutical products, clear demarcation has traditionally been required when multiple pharmaceutical wholesaling companies manage products in the same warehouse. The Company’s distribution center was the first in Japan to be licensed by the Tokyo Metropolitan Government as a joint distribution and delivery center for pharmaceutical wholesalers, by completely managing the storage location of pharmaceuticals by computer in an automated warehouse. We are currently conducting joint distribution with SAKAI MEDICINES CO., LTD.
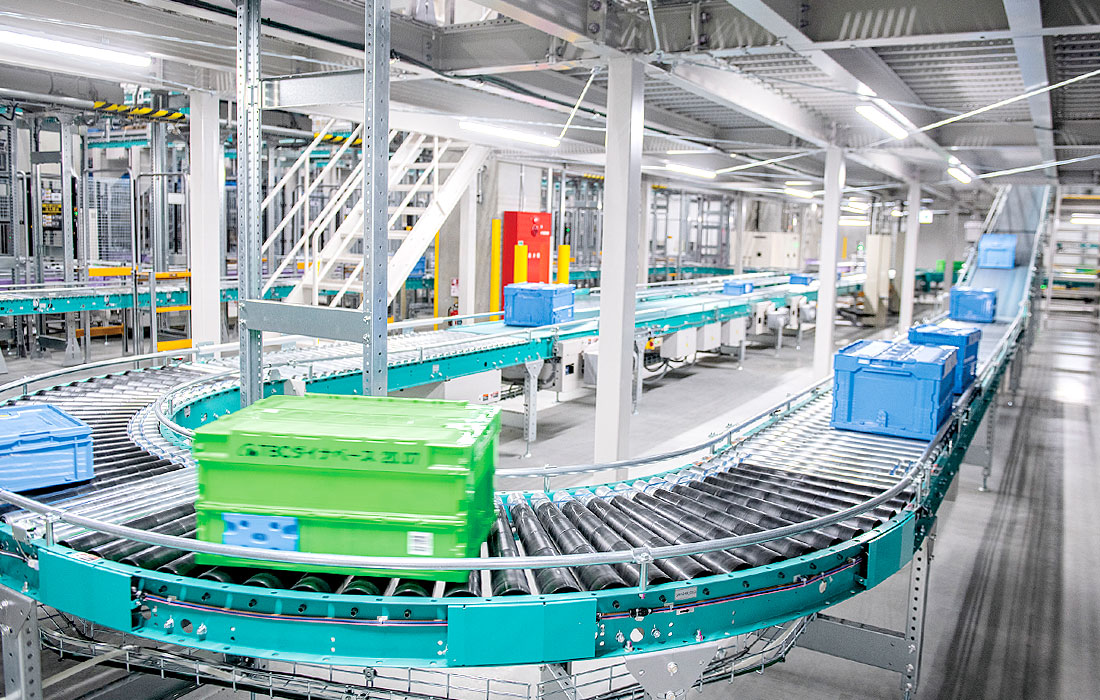
Pursuit of accuracy, lot management and continuity
We have built a delivery system that greatly contributes to the operational efficiency of our customers, boasting remarkable shipping accuracy thanks to state-of-the-art robotic technology and other advanced material handling equipment*.
*Material handling equipment: Efficient management of the entire process
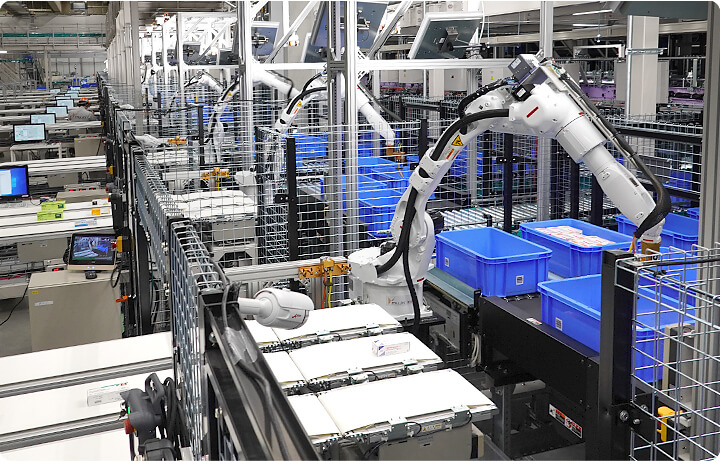
Robot picking automation rate
95%
TBC DynaBASE has introduced 34 robots. We have achieved a 95% piece-picking rate by robots.
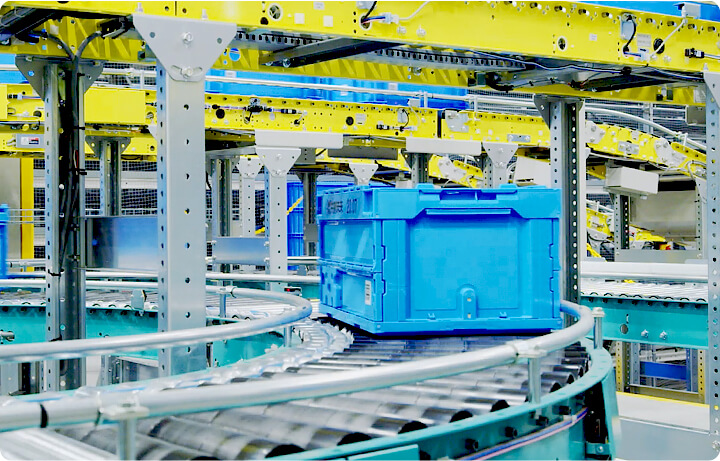
Shipping accuracy
99.99999%
(“seven nines”)
We strive for accuracy through the introduction of cutting-edge technology, and have achieved a shipping accuracy of 99.99999% (“seven nines”).
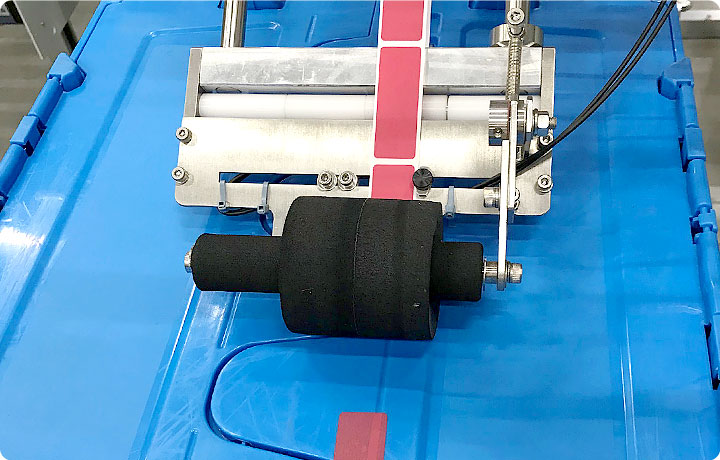
Improve operational efficiency of customers
No-inspection system
Based on the high shipping accuracy, we are promoting a no-inspection system, which allows the omission of inspections at the time of delivery. The sealing tape, which reveals letters when peeled off, ensures that the package remains unopened until delivery.
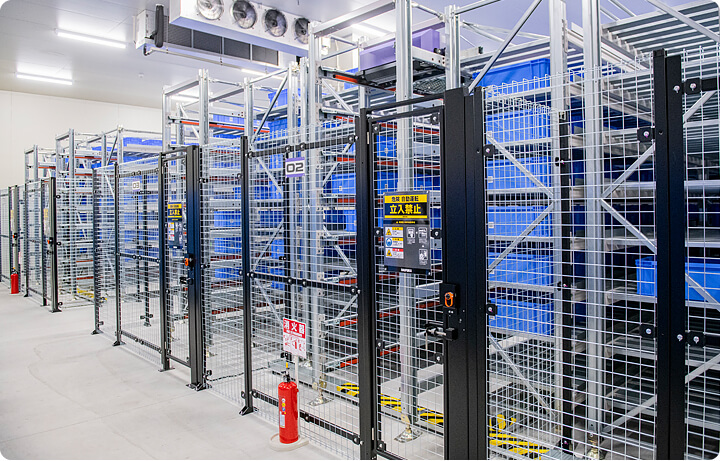
Cold storage unit
Products that need to be handled in a cold room are stored in a cold storage unit with an automated warehouse system. We have installed a system that monitors the internal temperature, thereby conducting thorough temperature control.
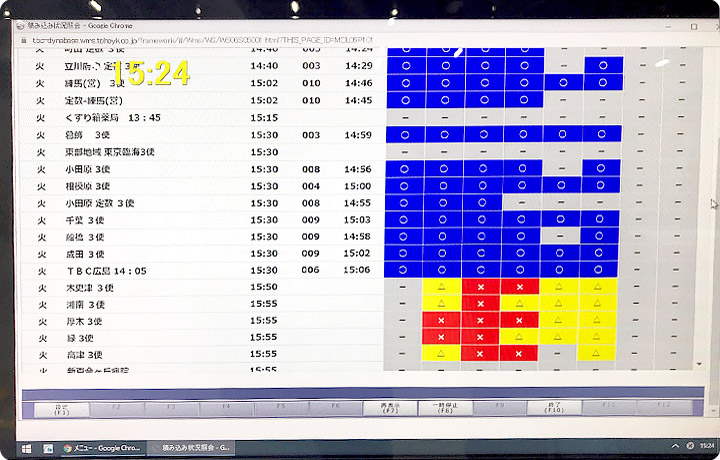
Direct delivery from the center
In order to shorten the lead time between ordering and delivery, we are actively promoting direct delivery from the center (delivery without going through the sales office).
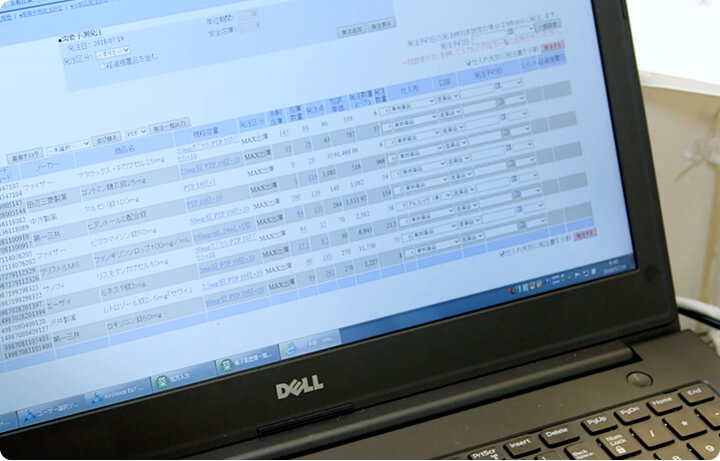
Planned deliveries of pharmaceuticals
We are improving the efficiency of delivery by planned deliveries in conjunction with an automatic ordering function of MIZAR, a pharmacy headquarters system that centrally manages inventory.
Next-generation distribution facilities that are friendly to people and the environment
TBC DynaBASE is actively engaged in quality control, security enhancement, and the reduction of environmental impacts, which are the responsibilities of a large, high-performance distribution center.
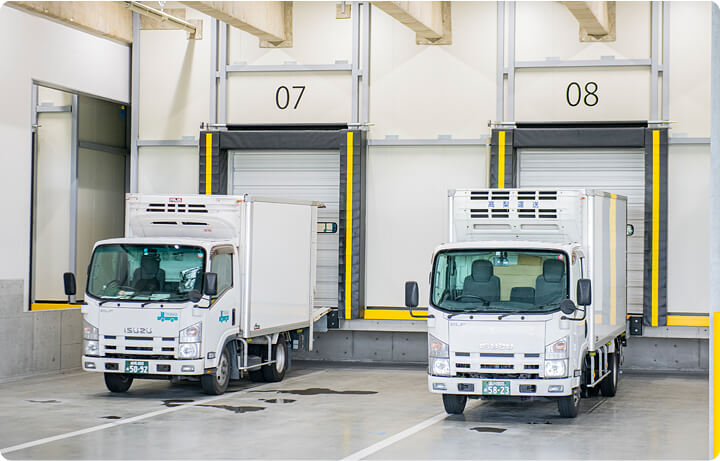
Establishment of a distribution system in compliance
with GDP Guidelines
Doors for delivery vehicles are fully equipped with dock shelters to reduce the influence of outside air and prevent foreign matter from getting inside. In addition, temperature loggers have been installed at various locations in the warehouse, and a 24-hour alarm system is in place to report any temperature deviations. We have also developed a quality-control environment that fully complies with Good Distribution Practice (GDP) Guidelines, including the installation of bird-proof nets and insect traps.
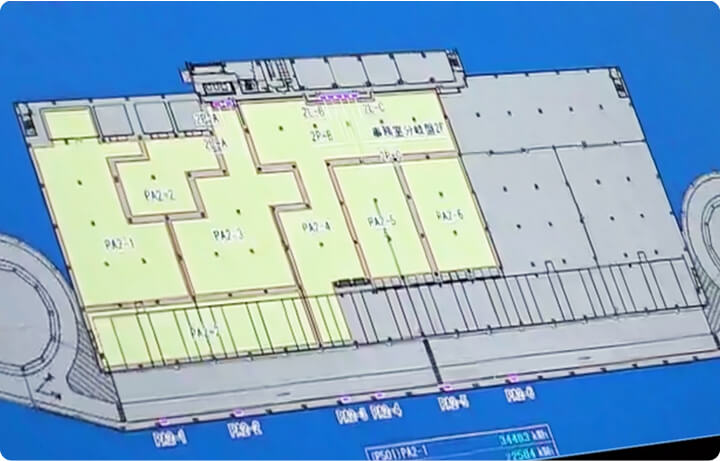
Reduce environmental load
We are working to reduce energy consumption through the use of nighttime power for picking robots and the introduction of BEMS.
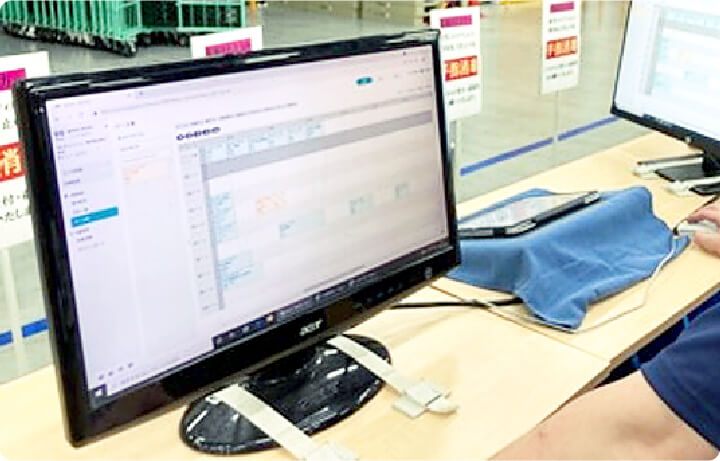
Truck reservation service
By introducing a truck reservation service utilizing a cloud-type berth management system, a driver waiting time of “0” is realized. We are working to improve the efficiency of cargo handling and reduce the burden on drivers.